Metoda PVT e kultivimit të kristalit të gjatë me rezistencë ndaj karabit të silicit në furrë me kristal lingote SiC 6/8/12 inç
Parimi i punës:
1. Ngarkimi i lëndës së parë: pluhur (ose bllok) SiC me pastërti të lartë i vendosur në fund të enës së grafitit (zona e temperaturës së lartë).
2. Mjedis vakumi/inert: zbrazni dhomën e furrës me vakum (<10⁻³ mbar) ose kaloni gaz inert (Ar).
3. Sublimim në temperaturë të lartë: ngrohje me rezistencë deri në 2000~2500℃, zbërthimi i SiC në Si, Si₂C, SiC₂ dhe përbërës të tjerë të fazës së gaztë.
4. Transmetimi në fazën e gaztë: gradienti i temperaturës nxit difuzionin e materialit në fazën e gaztë në rajonin e temperaturës së ulët (skaji i farës).
5. Rritja e kristalit: Faza e gaztë rikristalizohet në sipërfaqen e Kristalit të Farës dhe rritet në një drejtim të drejtuar përgjatë boshtit C ose boshtit A.
Parametrat kryesorë:
1. Gradienti i temperaturës: 20~50℃/cm (kontrolli i shkallës së rritjes dhe dendësia e defektit).
2. Presioni: 1~100mbar (presion i ulët për të zvogëluar inkorporimin e papastërtive).
3. Shkalla e rritjes: 0.1~1mm/orë (duke ndikuar në cilësinë e kristalit dhe efikasitetin e prodhimit).
Karakteristikat kryesore:
(1) Cilësia e kristalit
Dendësi e ulët e defekteve: dendësia e mikrotubulave <1 cm⁻², dendësia e zhvendosjeve 10³~10⁴ cm⁻² (përmes optimizimit të farës dhe kontrollit të procesit).
Kontroll i tipit polikristalin: mund të rritet 4H-SiC (rrjedha kryesore), 6H-SiC, përqindja 4H-SiC >90% (nevojitet të kontrollohet me saktësi gradienti i temperaturës dhe raporti stekiometrik i fazës së gaztë).
(2) Performanca e pajisjeve
Stabilitet në temperaturë të lartë: temperatura e trupit të ngrohjes prej grafiti >2500℃, trupi i furrës përdor dizajn izolimi me shumë shtresa (siç është grafiti i ndjerë + xhaketë e ftohur me ujë).
Kontrolli i uniformitetit: Luhatjet aksiale/radiale të temperaturës prej ±5 °C sigurojnë qëndrueshmërinë e diametrit të kristalit (devijimi i trashësisë së substratit 6 inç <5%).
Shkalla e automatizimit: Sistem kontrolli i integruar PLC, monitorim në kohë reale i temperaturës, presionit dhe shkallës së rritjes.
(3) Përparësitë teknologjike
Shfrytëzim i lartë i materialit: shkalla e konvertimit të lëndës së parë >70% (më e mirë se metoda CVD).
Pajtueshmëria me madhësi të mëdha: Prodhimi masiv prej 6 inçësh është arritur, ndërsa modeli 8 inçësh është në fazën e zhvillimit.
(4) Konsumi dhe kostoja e energjisë
Konsumi i energjisë i një furre të vetme është 300~800kW·h, duke përbërë 40%~60% të kostos së prodhimit të substratit SiC.
Investimi në pajisje është i lartë (1.5 milionë 3 milionë për njësi), por kostoja e substratit për njësi është më e ulët se metoda CVD.
Aplikacionet kryesore:
1. Elektronikë e fuqisë: Substrati SiC MOSFET për inverterin e automjeteve elektrike dhe inverterin fotovoltaik.
2. Pajisjet Rf: stacioni bazë 5G GaN-mbi-SiC substrat epitaksial (kryesisht 4H-SiC).
3. Pajisje për mjedise ekstreme: sensorë për temperaturë të lartë dhe presion të lartë për pajisjet e hapësirës ajrore dhe energjisë bërthamore.
Parametrat teknikë:
Specifikimi | Detajet |
Përmasat (Gj × Gje × Lartësi) | 2500 × 2400 × 3456 mm ose personalizoni |
Diametri i enës së shkrirjes | 900 mm |
Presioni maksimal i vakumit | 6 × 10⁻⁴ Pa (pas 1.5 orësh vakum) |
Shkalla e rrjedhjes | ≤5 Pa/12 orë (pjekje) |
Diametri i boshtit të rrotullimit | 50 mm |
Shpejtësia e rrotullimit | 0.5–5 rpm |
Metoda e ngrohjes | Ngrohje me rezistencë elektrike |
Temperatura maksimale e furrës | 2500°C |
Fuqia e ngrohjes | 40 kW × 2 × 20 kW |
Matja e temperaturës | Pirometër infra të kuq me dy ngjyra |
Diapazoni i temperaturës | 900–3000°C |
Saktësia e temperaturës | ±1°C |
Diapazoni i presionit | 1–700 mbar |
Saktësia e Kontrollit të Presionit | 1–10 mbar: ±0.5% FS; 10–100 mbar: ±0.5% FS; 100–700 mbar: ±0.5% FS |
Lloji i Operacionit | Ngarkim nga poshtë, opsione sigurie manuale/automatike |
Karakteristikat opsionale | Matje e dyfishtë e temperaturës, zona të shumëfishta ngrohjeje |
Shërbimet XKH:
XKH ofron të gjithë shërbimin e procesit të furrës SiC PVT, duke përfshirë personalizimin e pajisjeve (projektimi i fushës termike, kontrolli automatik), zhvillimin e procesit (kontrolli i formës së kristalit, optimizimi i defekteve), trajnimin teknik (operimin dhe mirëmbajtjen) dhe mbështetjen pas shitjes (zëvendësimin e pjesëve të grafitit, kalibrimin e fushës termike) për të ndihmuar klientët të arrijnë prodhim masiv të kristalit sic me cilësi të lartë. Ne gjithashtu ofrojmë shërbime të përmirësimit të procesit për të përmirësuar vazhdimisht rendimentin e kristalit dhe efikasitetin e rritjes, me një kohë tipike prej 3-6 muajsh.
Diagram i detajuar
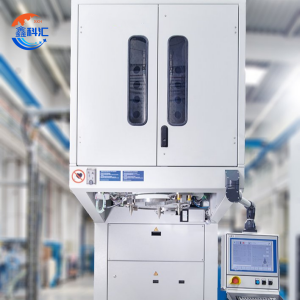
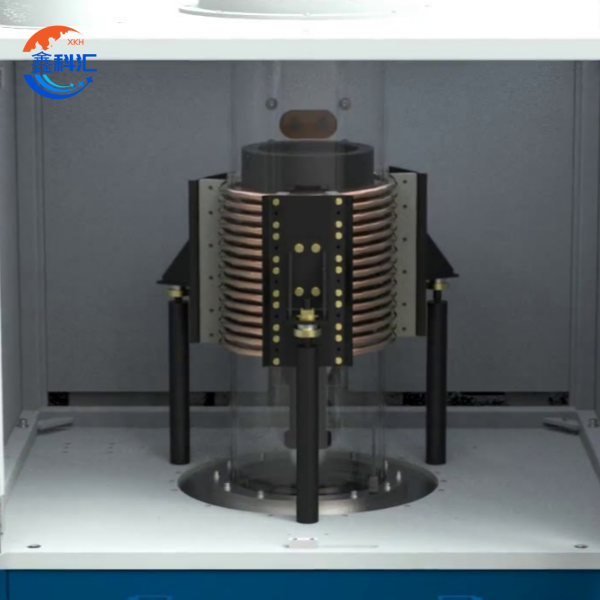
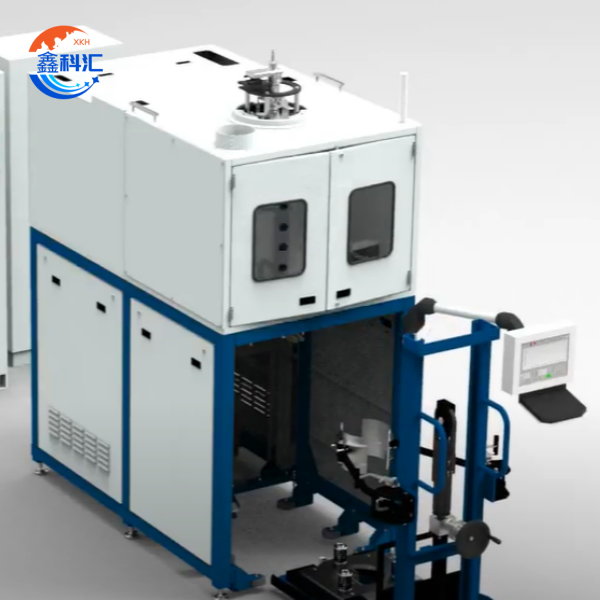